Empowering
Kanban Empowered Inventory Management for B2C
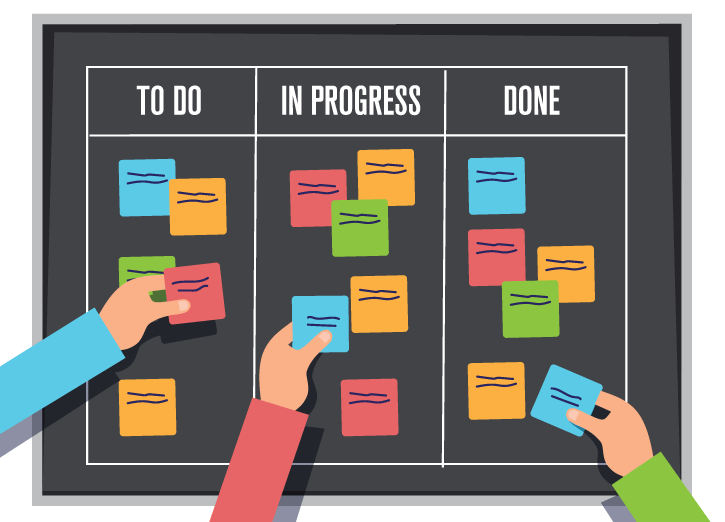
46% of SMBs in the U.S. don’t track their inventory or use manual methods such as excel spreadsheets to manage inventory. An effective inventory management system is an advantage that few would like to ignore.
A kanban inventory system can give you that edge by ensuring companies maintain minimal supplies to reduce spoilage and prevent waste.
Taiichi Ohno of Toyota Automotive developed the first Kanban inventory system; the aim was to understand inadequate & incompetent production and control inventory optimally. The JIT or “just-in-time” strategy is at the centre of the Kanban inventory management system, which prompts manufacturing only “what is needed” and “when it is needed” to reduce costs and then use Kanban to signal when replenishment is required. This limits manufacturing and focuses on improving your processes and workflows to remove bottlenecks and waste while enhancing the quality.
And retailers (b2c, d2c) and manufacturers can undoubtedly learn to implement Kanban for their inventory management system. Some expected benefits realized by the factory, warehouse, shipping, and logistics managers:
- Less overhead costs
- Apt progress reports
- Controlled execution of processes
- Increased efficiency
- It improves flow and teamwork and reduces response time
- Agility towards change
- Prevents overproduction that leads to reduced waste and outdated inventories
While rolling out Inventory management using Kanban, Toyota gave six guidelines to follow –
- Never Pass Defective Products: Upstream processes must create policies for quality and compliance checks.
- Take only What’s Needed: Downstream processes only take what is needed to prevent overproduction. Using historical data, forecast inventory to lower costs and reflect market demands.
- Produce Exact Quantity: Avoid overproduction, which leads to excess inventory and more costs. Using historical data, forecast throughput needed for a given period and added some %age buffer which should vary basis the previous cycle’s input.
- Level the Production: Keep production to capacity to achieve a steady workflow. Kanban should be detailed enough to help you visualize the production line and identify bottlenecks and delays.
- Fine-Tune and Optimize Process: Explore ways to add efficiencies and remove bottlenecks after implementing Kanban, given that Kanban will give visibility to the process and identify areas to improve.
- Stabilize the Process: Maintain quality, revisit policies and optimize processes to gain stability so you can standardize.
- Attach Kanban: A Kanban should accompany each item every time. These cards contained the information that identified each batch of material: SKU, code, lot size, destination, customer that requested it, etc. The cards are hung on each container or shelf holding the product.
To help keep estimating less stressful and time consuming, we can use the following method to calculate the number of Kanbans or the initial WIP limit for production:
Number of Kanban = DT(1+x)/C
- D: Demand per unit of time
- T: Lead time
- C: Container capacity
- X: Buffer, or safety factor (%age buffer)
Imagine a demand for 100 tapes/day (on average).
The lead time to obtain new tapes once the signal starts at the upstream (or supplier) and the tapes is five days.
The Safety Stock in percentage is 20% (to compensate for demand variation or delays)
Every container capacity is 50 tapes.
Number of Kanban = 100 * 5 * (1+20) / 50 = 12 Kanban
What does it mean?
It means that 12 Kanban (WIP Limit) must be present between upstream and downstream to deliver 100 tapes per day.
Limiting WIP is the key to Kanban, and it’s what makes it valuable. By balancing the amount of WIP to the capacity, Kanban enables clear focus and vision into work throughout production and more rapid output. Implementing Kanban is not about cutting corners but finding an efficient way of executing your workflow. But it might make the process slow for some time; ups and downs can be expected (J-curve effect). The moment things are streamlined, it will start showing results.
Case Study:
Problem — A Furniture manufacturing company in India was struggling to
- Manage raw material inventory
- Ensure orders are delivered on time
- Get an overview of their manufacturing process
Solution: A physical Kanban Board tailored to their complex manufacturing needs was designed to help them manage the business and streamline operations from sales orders to mass-produced goods to delivery.
Benefits –
- Improve on-time order fulfilment by nearly 32%
- Optimize overall inventory by 20%
- The efficiency of their day-to-day operations went up
- Visibility of stock and inventory
A robust Kanban inventory system can manage the complete supply chain across multiple business departments. The Kanban system should be managed by a cross-functional team, enabling stakeholders to act on real-time data. In today’s digitally driven world, implementation of the Kanban no longer involves physical cards: a warehouse management system in combination with automatic identification systems, such as barcodes and Kanban cards which helps extract information linked to SKU when scanned. A sound Kanban system can signal replenishment and ensure the production line is working at total capacity and has no wastes.
Please don’t hesitate to contact me if you have more questions about implementing Kanban for your inventories.