Empowering
Streamlining Financial Processes and Optimizing Operational Efficiency for a Global Cement Manufacturer
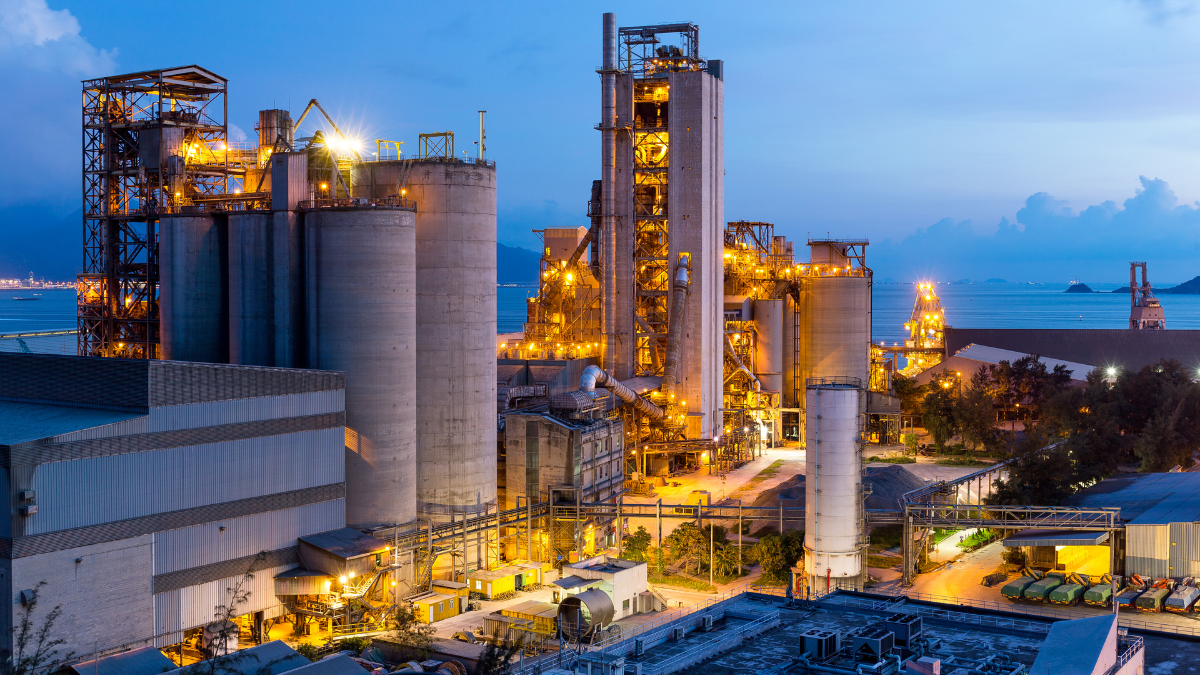
Client: A top global cement manufacturer with a heritage of leading marble partners, delivering premium quality cement. The company focuses on technological excellence, ensuring impeccable quality and effective communication. With an extensive dealer and retailer network, they are positioned as a preferred brand in the premium cement market.
Problem Statement:
The client encountered several operational bottlenecks that impeded their scalability and efficiency. Its complicated financial processes, lack of coordination between departments, and inventory management issues were significant hurdles. Additionally, the company struggled with implementing a costing module in their ERP system and faced productivity issues due to the high number of active users on their ERP systems impacting their overall performance
Key Challenges:
Complicated Financial Processes: The client’s financial processes, including invoice generation, procurement, and other transactional activities, were complex and time-consuming, and created bottlenecks in financial operations, that led to inefficiencies and errors.
Lack of Inter-Departmental Coordination: There was a significant lack of coordination between their critical departments such as purchase, production, and sales, and this misalignment resulted in operational delays, miscommunications, and limited scalability.
Inventory Management: Efficiently tracking and managing raw materials and finished products was a major challenge for them where the inaccurate inventory data led to overstocking or stockouts, affecting production schedules and customer satisfaction.
ERP Integration and Customization: Integrating a complex costing module into their existing ERP system was challenging due to the dynamic nature of raw material costs and the need for extensive customization to meet specific business requirements.
Existing System Performance Issues: Their existing ERP experienced significant performance issues when a high number of users were active simultaneously. This slowdown affected productivity and operational efficiency, as employees faced delays and disruptions in their work.
Plant Maintenance: The complexity of maintaining plant equipment and ensuring minimal downtime was a significant challenge. Unplanned maintenance activities disrupted production schedules leading to unexpected downtimes and increased operational costs.
Freight Management: Efficiently managing freight logistics, including scheduling, routing, and cost optimization, was a critical concern for the client. Ineffective freight management Coordinating the transportation and delivery of raw materials and finished products was complex and resulted in high logistics costs and delays.
Cost Management: The client faced difficulties managing costs effectively across various operations. The need for accurate cost tracking and control mechanisms, including raw material, production, and transportation costs, was paramount to ensure profitability and competitive pricing, impacting the company’s profitability.
Material Requisition: Managing material requisitions for production processes was crucial and complex for the client, impacting production timelines and resource allocation. Manual processes led to delays, errors, and inefficient resource utilization for the business operations.
Solution:
BaffleSol Technologies provided Microsoft Dynamics 365 Finance and Operations’ comprehensive support for global cement manufacturer, addressing the unique business needs through customization and system integration, along with inventory management to improve their operational efficiency. The solution was rolled out in stages, starting with AX2009, upgrading to AX2012, and finally transitioning to Microsoft Dynamics 365 Finance and Operations (FinOps).
Modules:
ERP Integration and Customization: After integrating Microsoft Dynamics 365 Finance and Operations for the cement manufacturer with the existing systems, the ERP systems were extensively customized to streamline finance, operations, and inventory management as per business requirements. This customization included the implementation of a complex costing module that could handle dynamic raw material costs and provide accurate cost tracking.
Enhanced Inter-Department Communication:
- E-Sampark Portal: This portal was developed for the marketing team to enable dealers to create orders independently. This not only improved order accuracy but also reduced the workload on the sales team.
- Freshdesk Portal: It was implemented for IT support, the Freshdesk portal improved issue resolution times and provided a centralized platform for managing IT support requests, enhancing overall communication and coordination.
Productivity and Efficiency Improvements: By integrating the E-Sampark portal with the Microsoft Dynamics 365 ERP systems, the company was able to manage user load more effectively. This integration addressed the performance issues experienced with high active user numbers, ensuring smooth and uninterrupted operations.
Plant Maintenance Management:
- Maintenance Module: Implemented a maintenance management module within the ERP system to schedule and track maintenance activities for plant equipment and machinery. This module helped reduce unexpected downtimes and repair costs by ensuring timely and proactive maintenance
Freight Management:
- Transportation Module: Integrated a transportation management module to streamline the coordination of raw material and finished product deliveries. This module optimized logistics routes, reduced transportation costs, and minimized delivery delays.
Cost Management:
- Cost Control Module: Developed a comprehensive cost management module to monitor and control various operational costs. This module provided real-time insights into raw material costs, production costs, and transportation costs, helping the company make informed decisions to enhance profitability.
Material Requisition Module:
- Material Management: Implemented a material requisition module within Microsoft Dynamics 365 to streamline and automate the process of requesting and approving materials for production. This module enabled real-time tracking of material requests, significantly improving transparency and efficiency in resource allocation. By integrating with inventory management, it ensured accurate stock availability and facilitated more effective procurement planning.
Result:
Through the strategic assistance of Microsoft Dynamics 365 Finance and Operations for the cement manufacturer and the development of customized e-platforms, BaffleSol Technologies successfully addressed the complex challenges faced by the global cement manufacturer. The solutions provided not only streamlined financial and operational processes but also enhanced communication and coordination across departments, improved plant maintenance, optimized freight management, and provided robust cost management, paving the way for increased scalability and efficiency. As a result, the client achieved significant cost savings, experienced smoother operations and better resource management, increased scalability, and improved overall efficiency, solidifying their position as a leader in the premium cement market.